Top Five Ways to Reduce the Cost of Counting Your Inventory
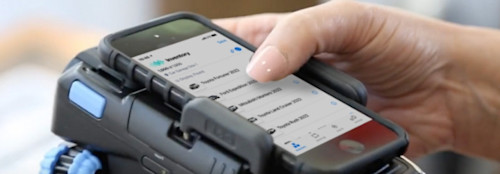
Many organizations hate counting their inventory; customers must wait while operations are halted, often for a week or more, to give way for counting. Staff is doing dull and monotonous counting, then data input follows the count, which might take an additional week. The inventory count and the data input procedure are vulnerable to inaccurate numbers.
No matter how you do your inventory and how your numbers are kept and maintained on your records, you will have to put effort into adjusting and making sure your count is accurate and correct.
Here are the top five ways to reduce the cost of counting your inventory more effectively, and reduce inventory costs.
Top Five: ABC Analysis
With ABC analysis inventory management approach, inventory items are valued according to how important they are to the company.
This method places stricter and frequent checks on class A items since they are significant to the company's sales performance. It's crucial to evaluate demand and ensure stock levels correspond to it continuously. It leads to better control of high-priority inventory and reduces inventory time and costs but compromises the overall accuracy of other items in the stock, which could result in customer dissatisfaction.
It will also demand substantial resources because "class A items" must be regularly analyzed to determine if they are still a high priority. If an inventory item is no longer consumed or demanded as often, it is transferred to a different inventory categorization. This systematic and frequent process review requires more extensive data monitoring and gathering.
Top Four: Cycle/Manual counting
Another simple and inexpensive technique to do your inventory counts is to cycle count. Staff often conduct cycle counts regularly, sometimes weekly or monthly, and count a portion of the overall inventory in a particular section of the warehouse. Although this may look like a quick and easy solution for managing inventory, it can be time-consuming and labor-intensive, considering that manpower is the main requirement for this process. Not to mention that because you are relying on your staff's counting and recording abilities, this method is also prone to error as there may be uncertainty on the records after the count if the same inventory item is kept in many locations.
Top Three: Just In Time
Just in Time, or "JIT" is an inventory-management strategy is an inventory-management strategy that intends to assist companies in keeping precisely the right amount of inventory on hand to satisfy client demands while avoiding excess.
This technique is a great way to lessen storage space and reduce waste. You don't need as much warehouse to keep items when the stock turns around more quickly.
The downside of this procedure is that JIT implementation could be too complicated and comprehensive since management has to re-evaluate its entire business and inventory operation. Everything has to be modified, from the transportation of materials from the manufacturers to the delivery of the final product. Smaller companies may find it challenging to deal with these logistical challenges, forcing you to split up big orders over a more extended period and even across numerous smaller suppliers.
Top Two: Barcode
The barcode method is widely used and is very common in most businesses. Even though application complexity varies, the price for each barcode label is just a few cents; this is another cost-effective medium to do inventory. But like cycle count, it could also be labor and time intensive as items must be scanned individually to get a direct line of sight.
Barcoding is also an old system. While it's still highly relevant in this age, other systems may take over in a few years.
Top One: RFID
You should invest in an RFID inventory management system to boost your profitability and reduce inventory costs simultaneously.
This technology will save you tons of time and labor by scanning more items simultaneously. In contrast to barcodes, RFID readers can scan multiple items at a certain distance allowing quick inventory processing and regular updates. With this, employee efforts on manual counting and human errors that might come with it will no longer be a problem and will reduce the budget being exerted on your inventory operations.
Taking advantage of this modern inventory system will allow you to have complete visibility of each item regardless of their inventory class/priority, including the number of stocks and locations you might have because all things are counted instead of only focusing on those that bring the most revenue. Thus, it gives you more time to confidently move products around and showcase them to customers. Knowing that you have all these in stock results in enhanced customer satisfaction.
The bottom line:
Keeping away from implementing the wrong inventory management process will always be as important as choosing and using the best system for your business.
Businesses must learn to utilize a system that gives accurate and improved inventory visibility with less effort and budget. Most importantly, without compromising customer satisfaction. These benefits are all found in implementing RFID in counting your inventory; it is the best way to reduce cost compared to all the processes mentioned above. RFID systems hold the best of all worlds in keeping track of your inventory while avoiding daunting and unnecessary operations.
We make it simple and easy
The retail world is changing. Many manufacturers and retailers are trying to find new and exciting ways to integrate their inventory data with RFID inventory systems. One of which is the Walmart mandate that recently expanded to many other supply chain verticals.
SimplyRFiD’s products and services, such as the Wave: Audit and Accurate Inventory Kickstart campaign, are the tools necessary to build a system where you can maximize the use of RFID technology in your business. We help retailers and manufacturers by guiding them through the proper methodology, execution, and maintenance of said systems.
Contact our sales team for a scheduled product demo and any other additional information.